Written By Adeel Abbas
A team of international researchers, led by Penn State, has discovered a new type of ferroelectric polymer that shows exceptional potential as a high-performance motion controller or actuator.
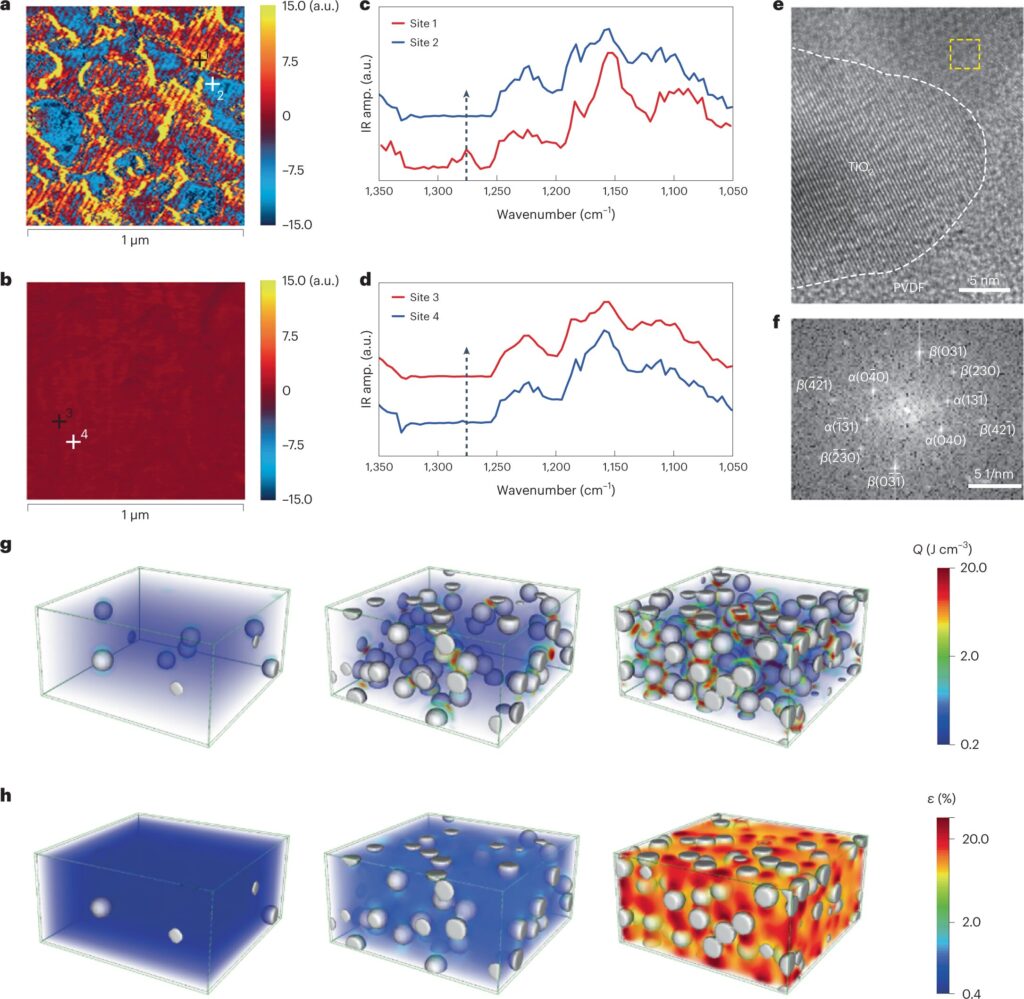
This polymer demonstrates a remarkable ability to convert electrical energy into mechanical strain, which is crucial for actuator materials that deform when an external force, like electrical energy, is applied. Unlike traditional rigid actuators, this soft ferroelectric polymer offers higher flexibility and adaptability.
The research highlights the capabilities of ferroelectric polymer nanocomposites in surpassing the limitations of conventional piezoelectric polymer composites. These nanocomposites hold promise for developing soft actuators with improved strain performance and mechanical energy density. Soft actuators, known for their strength, power, and flexibility, have captured the interest of robotics researchers.
The potential applications of this new ferroelectric polymer include medical devices, advanced robotics, and precision positioning systems. It could enable the creation of soft robotics, often referred to as artificial muscles, that closely mimic human muscle by combining high load-carrying capacity with large strains.
While there are obstacles to overcome, the study proposes potential solutions. Ferroelectrics are materials that exhibit spontaneous electric polarization when subjected to an external electric charge, causing positive and negative charges to separate. The phase transition in these materials during the conversion of electrical energy to mechanical energy can significantly alter their properties, making them suitable for use as actuators.
Traditionally, ferroelectric actuators have been made of ceramics, but ferroelectric polymers offer several advantages. These polymers can generate a significantly higher electric-field-induced strain, making them ideal for actuation. They also provide flexibility, reduced cost, and lower weight compared to other ferroelectric materials, which makes them attractive for soft robotics applications.
The study addresses two key challenges in the field of soft material actuation. Firstly, it focuses on enhancing the force generated by soft materials. While polymers exhibit large strains, they generate less force compared to piezoelectric ceramics. Secondly, ferroelectric polymer actuators typically require a high driving field to induce the shape change necessary for the ferroelectric reaction.
To address these challenges, the researchers developed a percolative ferroelectric polymer nanocomposite. They incorporated nanoparticles into a polymer called polyvinylidene fluoride, creating an interconnected network of poles within the polymer. This network facilitated the induction of a ferroelectric phase transition at much lower electric fields than typically required. By utilizing an electro-thermal method called Joule heating, which produces heat when electric current flows through a conductor, the researchers achieved the phase transition with less than 10% of the electric field strength typically needed.
The integration of strain and force into a single material, along with the use of Joule heating to drive the actuation, enables this new material to be effective at low driving fields. This breakthrough has significant implications for various applications requiring low driving fields, such as medical devices, optical devices, and soft robotics.
In summary, the research led by Penn State has unveiled a new ferroelectric polymer with immense potential as a high-performance actuator. By addressing challenges related to force generation and driving fields, the researchers have paved the way for the development of soft actuators with enhanced capabilities, making them suitable for a range of applications in fields like medicine, robotics, and precision positioning systems.
Read from original source
Yang Liu et al, Electro-thermal actuation in percolative ferroelectric polymer nanocomposites, Nature Materials (2023). DOI: 10.1038/s41563-023-01564-7